3d Printing Concrete Design Cad
- Research
- Open Access
- Published:
Development of a 3D Printer for Concrete Structures: Laboratory Testing of Cementitious Materials
International Journal of Concrete Structures and Materials volume 14, Article number:13 (2020) Cite this article
-
13k Accesses
-
9 Citations
-
Metrics details
Abstract
This study deals with (a) the development of a prototype 3D printer for concrete structures having a bed size of 1 × 1 × 1 m for a laboratory testing and (b) laboratory testing of cementitious materials with different design mixes to find their suitability and efficacy for the developed 3D printer. In this printer, a program with the concept of computer numerical controlled milling was adopted to control the nozzle motion using an easy graphic user interface program. The experiment was carried out to test mechanical control and proper material properties of the printer. Thus, the optimum values of water-cement ratio of cementitious materials for the 3D concrete printer were determined by experimental trials. Also, the adequate viscosity of the material for layering and dispensing is determined by a slump-flow test. The suitable size of sands for the dispensing system was found through the trials. However, shrinkage cracks occurred during the hardening process for the paste and mortar that polyvinyl alcohol fibers are added to prevent the cracking and build an improved quality 3D printed structure. After suitable and efficient mix ratio is found, compressive strength is measured for the mechanical property. The experiments demonstrated possibility of printing concrete structure using the 3D printer.
Introduction
Over the last few decades, additive manufacturing, widely known as 3D printing, has drawn the attention of researchers from all over world for its capability to transform a drawing into an object. 3D printing is a technology that transforms three-dimensional digital drawings into three-dimensional shapes as desired by the users via a 3D printer (Wang et al. 2017; Stansbury and Idacavage 2016; Malaeb et al. 2015).
3D printing technology, which has been previously used for industrial design and manufacturing, is expanding its horizon to other fields like medicine, food, and construction (Henke and Trreml 2013; Tumbleston et al. 2015; Lee et al. 2017). The idea of 3D printing has also attracted the attention of engineers and architects, the possibilities of its use seem boundless. As the construction industry has adopted the new technology, its usage is extended to the final production of structure which is beyond making quick prototypes. Building structures through 3D printing has become a reality and often introduced by mass media (Seo et al. 2014; Bos et al. 2017). Yet 3D printing is still in its infancy level and its application is limited to certain areas because of technical weaknesses. Specifically, in the construction industry, further study is required to find out accurate mechanical control, suitable printing materials, and dispensing system using those materials (Shakor et al. 2017; Perrot et al. 2016; Gosselin et al. 2016).
In addition, technical limitations such as rising production costs of unstructured buildings and time-consuming construction methods are great challenges in the construction industry (Bos et al. 2016; Kazemian et al. 2017; Wei et al. 2018). According to Seo et al. (2014), 3D printing technology for construction is a possible approach to expand the horizon of construction. The 3D printing construction can be applied to producing not only massive and rapid structures but also a various types of structures such as atypical and user-customized designs with high complexity and diversity (Lee 2017; Asprone et al. 2018).
When 3D printing technology is used in construction, it is possible to secure a simple manufacturing and production system without going through entire construction stages. This would lead a new paradigm of construction allowing users to perform construction based on their own ideas by simple manufacturing and production systems. Also, the construction period and cost can be greatly reduced without going through unnecessary manufacturing steps (Lee2017; Kim 2017; Ahmed et al. 2016).
In this research project, a lab-scale 3D printer for printing concrete structures is developed with a mechanical system to control the movement of material dispenser. A material study was carried out to find out the idealized mixture for the system. The experiments were focused on finding out the efficient mixing ratio of cementitious materials used in the production of physical objects layer-by layer using the 3D printer. The printer showed great potential in the construction and architecture fields. With further improved 3D printing technology, automation or even autonomous construction seems feasible.
Development of a 3D Printer for Concrete Structures
A prototype model of 3D printer is developed and used to verify its performance before developing a full-fledge industrial scale model. In this study, a prototype printer with a smaller bed size of 1 × 1 × 1 m was designed. It is almost impossible to apply the smaller scale 3D printer to a construction project. Yet, it appears imperative that the prototype printer would be used to optimize motion control of the machine, to study the material properties of the printed objects, and to understand the dispensing mechanism. The 3D concrete printer requires the use of adequate material that is steadily dispensed with accurate control over nozzle movement to print a structure without any difficulties or defects. Therefore, this study focuses on the development of a 3D printer for concrete structures with three main targets of (i) motion control in 3D space, (ii) material properties of 3D printed objects and (iii) development of a material dispensing system. For research purposes, a prototype model of a 3D concrete printer was considered to be suitable for printing parts large enough to examine structural properties at a lab scale. The overall design of the 3D printer is shown in Fig. 1. The Fig. 1a shows a primitive concept design of the expected dynamics of 3D concrete printers, which was developed and adopted for the present study.
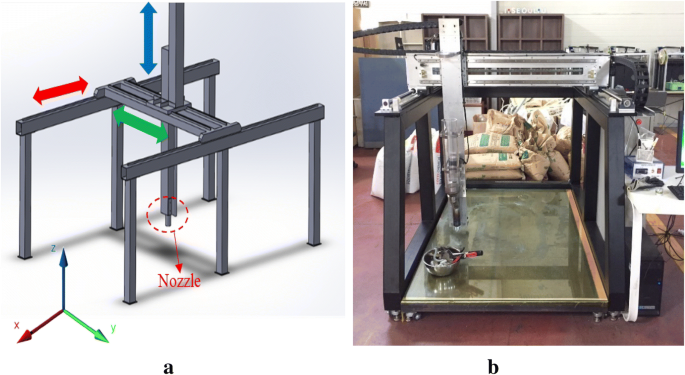
a Primitive concept design and b developed of 3D concrete printer.
Full size image
Motion Control
While various coordinate systems are available for motion control, either Cartesian coordinates or cylindrical coordinates are widely used for its efficiency and simplicity. A Cartesian Fused Deposition Modeling (FDM) 3D printer was selected for this research for its simplicity in control and practicality. Within the space set by frames, the movement of the printer is easily controlled and indicated through only linear motion control (Malaeb et al. 2015; Gosselin et al. 2016; Le et al. 2012). As Fig. 1a shows, the nozzle is installed on Z-axis of the moving frame that moves to both X and Y axis to print concrete structures. Each axis relies on a servo motor for the linear movement. Although frames could be obstacles limiting the workspace, they usually firm the entire system and secure accurate movement. Moreover, it is easy to extend the area of printing by adding an additional axis by installing a rail under the printer.
A software program was developed to control the movement which is similar to those used in mechanical machining devices with computerized numerical control (CNC) programs. When the program accepts a G-code for the movement control, the G-code gives an order to machine tools to control the nozzle motion. Basically, the idea of CNC milling is adopted in 3D printer nozzle motion (Le et al. 2012; Paul et al. 2018). This program can be generated by any materialization software of 3D printers. As shown in the Fig. 2, all the necessary variables for control such as movement speed, nozzle coordinates and nozzle speed can be adjusted on the Graphic User Interface (GUI) panel of the program.
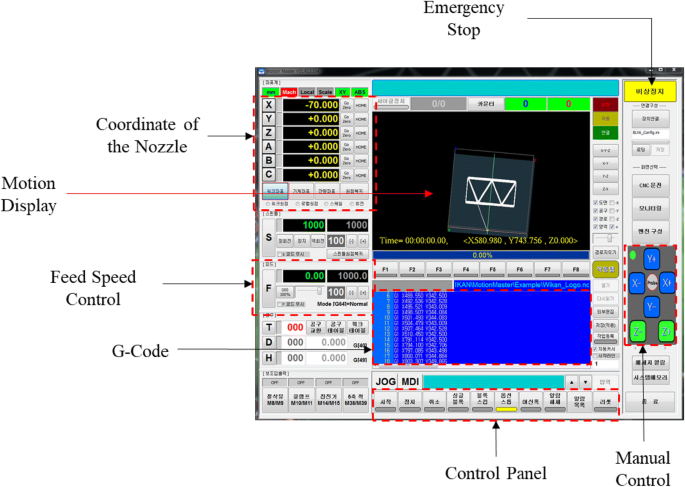
Program for the developed 3D printer.
Full size image
Dispensing System
The dispensing system is the most important technical part of a 3D printer to convey an adequate and consistent amount of concrete. This indicates that the control in the dispenser system should be optimized for extrusion based on the relevant properties of materials such as their stacking properties and compressive strength. For the dispensing system, screw type and pump feeding type were tested for extruding cementitious materials. The screw type nozzle provided better material control and constant extrusion of cementitious materials while the pump feeding type was difficult to control layering the materials.
Therefore, the 3D printer adopted screw type nozzle which was adequate to give extruding forces within the dispensing system. As Fig. 3 demonstrates below, the properties of the designed screw are total length of screw (L), which is 300 mm; pitch of the screw (Pc), which is 48 mm; diameter (D), which is 50 mm; and angle of blades is 19°. Also, screws were designed with different ratios of pitch to diameter (Pc/D), and a screw with a ratio around 0.96 yielded extrusion with sufficient pressure to extrude conventional mortar. This factor is directly related to the rotational speed of the screw since the amount of material extrusion is to be controlled by modifying the speed for consistent layer building.
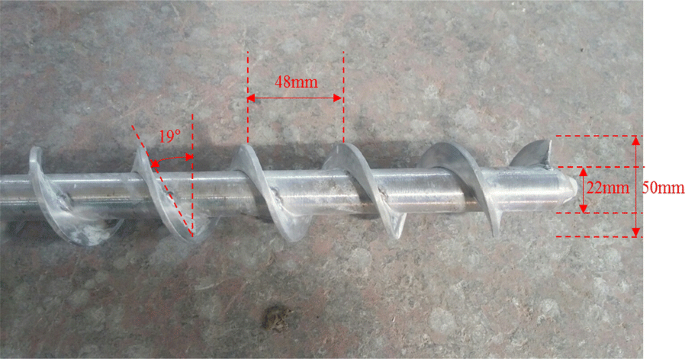
Designed screw for the 3D printer.
Full size image
Printing Process
The printing process of a 3D printer for concrete structures is primarily composed of three stages: printing preparation, material preparation, and printing. In the printing preparation stage, a desired printing component is designed in a 3D CAD model to convert the model to an STL file format. From the file, the printing path of the component is generated to create a G-code file. After the G-code file is created, the printing preparation stage is completed for the printer. The next stage involves mixing of concrete or cementitious materials for the printing. The materials are placed into the hopper to provide the materials to the pump and nozzle constantly. When the materials are prepared, the printing is processed using hopper-pump-nozzle system that schematic of the printing is shown in Fig. 4. In the system, two regulators are installed to control the pump and a screw from the nozzle. Therefore, two systems can be controlled to print the component constantly and stably.
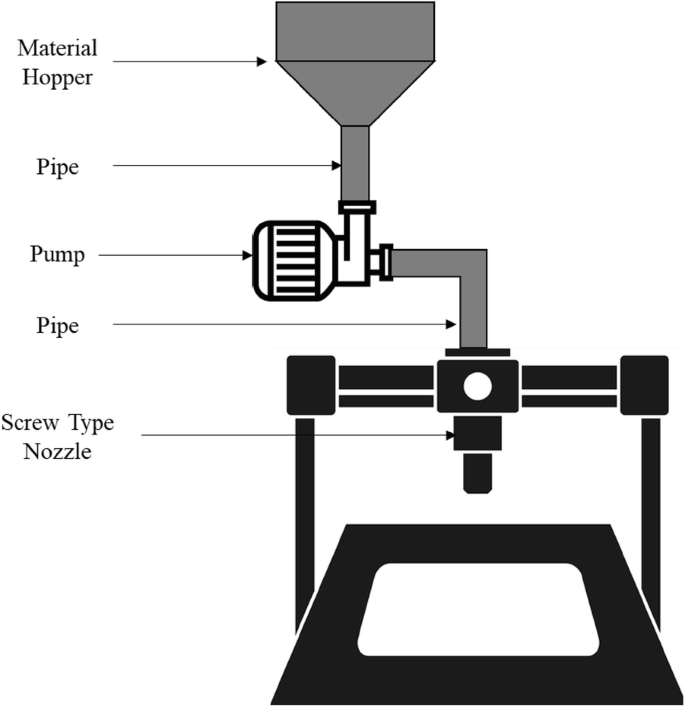
Schematic of a printing process for the 3D printer.
Full size image
Functional Testing
After development of a 3D printer for concrete structures is completed, its printing capability and function were tested focusing on the layering and dispensing of the cementitious materials. Experimental trials were performed by printing a hollow wall design (580 × 320 mm), as shown in Fig. 5. An important aspect of the test was to find out material properties and mechanical control by examining the layering condition of cementitious materials and its hardening process.
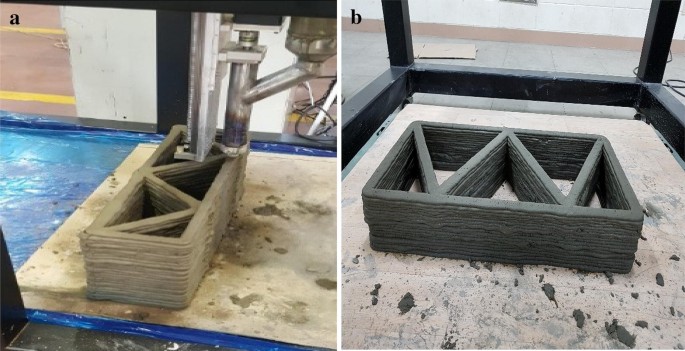
a Printing of a hollow wall using the 3D printer and b printed hollow wall for functional testing of the 3D printer.
Full size image
In the experiments, paste, the mixture of cement and water, was used to find the optimum value of W/C ratio and efficient viscosity for the layering and dispensing of the cementitious materials. Then, mortar which is composed of paste and sand was tested by adding different sizes of sand to find efficient size and ratio of sand from the suitable ratio of the paste. After finding the suitable sand size and ratio of sand, PVA fibers were included in the mix to improve buildability of the printing. Different ratio of PVA fibers were tested to find the optimal mix for the printing of cementitious material. Also, the slump-flow tests for each tested material were performed to seek an efficient viscosity of the materials from the values of slump flow spread. Then, hollow walls are printed with each cementitious material. Therefore, the appropriate mix design ratio for the printer was determined and tested from the result of experiments. After finding optimal mix ratio for the cementitious materials for the printing, mixtures' compressive strength is determined using BS 1881-116:1983.
Throughout the functional testing, an ordinary commercial general type 1 cement was used. Two sizes of sand, maximum size of 0.8 mm and 0.7 mm, and polyvinyl alcohol (PVA) fibers were used to determine a suitable and efficient mix design ratio for the printer to print the hollow wall. Before the printing of each hollow wall with the different mix design, a trial run of cementitious materials using the 3D printer was participated to determine settings of the printing such as motion speed of the nozzle, a rotational speed of a screw and height of the nozzle. During the experimental trials, the diameter of the nozzle tip was 30 mm, and the bed size corresponding to the total range of the nozzle movement on each axis was 1 × 1 × 1 m.
Results and Discussion
For functional testing, three different types of mix designs: (1) cement and water, (2) cement, water and sand, and (3) cement, water, sand, and PVA fibers were used to find optimum mix ratios for dispensing and layering the cementitious materials and print three hollow walls. During the experiments, three aspects of the 3D printing of cementitious materials are studied: a material aspect, a control aspect, and other aspects found during the experiments.
Material Aspect
Initially, the paste was used to find an efficient slump flow spread value for dispensing and layering the cementitious materials. Since material viscosity is the most important factor for clear dispensing and layering, a slump-flow test was used to find an optimum slump flow spread of materials before printing. Table 1 summarizes the different mix design ratios used for functional test and the slump-flow test is performed for each ratio.
Full size table
The first mix, the mix design 1-1, had a slump flow spread of 220 mm at which the paste was dispensed; unfortunately, layering did not occur because of inconsistent dispensing. The paste was watery and produced inconsistency in the extruded material. Therefore, in the second mix design, the water-cement ratio (W/C) was decreased to have more control on the flow value. In this case, the flow value was maintained at a minimum value of 190 mm, which become a firm. A cement paste with a slump flow spread of 185 mm, the mix design 1-4, was tested, but the material was too stiff to be dispensed without clogging the nozzle. However, the mix design 1-2 and 1-3 with W/C ratios of 0.32 and 0.30, respectively, were continuously dispensed and successfully layered the materials. The printed wall using the materials was stable despite some defects caused by shrinkage cracking, as shown in Fig. 6.
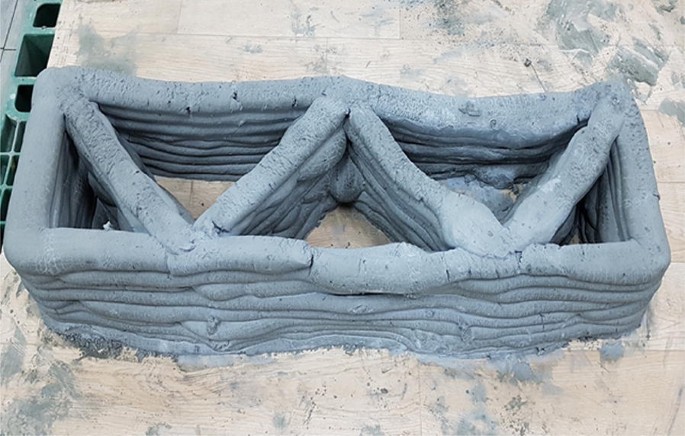
Constructed hollow walls with the paste.
Full size image
The printer took approximately 10 min to print a 63 mm high wall composed of 9 layers. These experimental trials showed that W/C ratio and slump flow spread should be maintained between 0.30 to 0.32 and 190 to 200 mm, respectively, for optimum extraction, dispensing, and proper layering of the cementitious materials.
First experiment was focused on determining proper material properties of the cement paste to find adequate condition of cementitious materials for layering and dispensing. The second experiment was conducted to increase workability and the strength by adding the sand to determine printable size of sand. Table 2 summarizes the different mix ratios used for the second experiments using mortar.
Full size table
First, sand size I (particle size less than 0.8 mm) was tested for the mix design 2-1 with half the amount of cement and caused clogging in the nozzle. The sand was tested again for the mix design 2-2 with less amount and the clogging occurred 3 min after the printing time. Therefore, sand size II (particle size less than 0.7 mm) was used for the mix design 2-3 but the clogging occurred in the nozzle part approximately 12 min after the printing time as shown in Fig. 7a. Then, the sand was re-tested with less amount and the wall were successfully printed with the mix design 2-4. According to the experiment, adding 0.4 more amount than a cement for 0.7 mm maximum size sand is recommended for the 3D printer. However, mortar layers were successfully layered over each other, some of the layers cracked during hardening as shown in Fig. 7b.
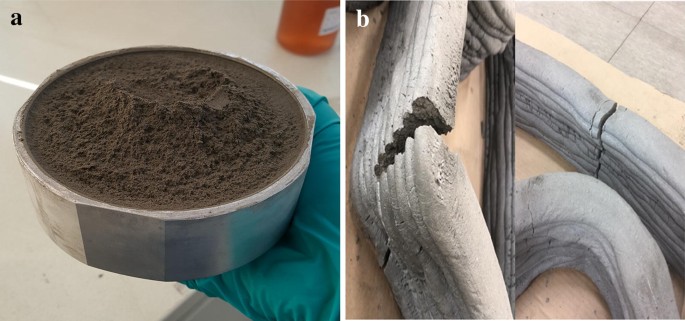
a Clogging occurring in the nozzle and b cracks occurring during hardening.
Full size image
Since shrinkage cracks occurred in the previously printed constructed walls, further experiments were performed by adding PVA fiber in mortar mix so that cracking can be avoided in 3D printed hollow walls to improve their stability. The PVA fibers were added in varying amounts of 6 g, 4 g, and 2 g successively, which corresponds to 0.3%, 0.2%, and 0.1%, respectively, from the cement of the mix designs. The corresponding mix designs with varying PVA fiber amount are summarized in Table 3.
Full size table
Although the mix designs met the optimum slump flow spread value for dispensing and layering of the materials, the screw inside of the nozzle compartment malfunctioned when the mortar contained more than 0.2% of PVA fibers. The printing was stopped after 9 min and 12 min of printing for the mix design 3-1 and 3-2, respectively, because screw was clogged with continuous gathering of fibers in the nozzle that interrupted dispensing the materials. However, the mix design 3-3 successfully layered with 0.1% PVA fiber and did not cause clogging in the nozzle compartment. In order to increase the continuous printable time, materials were adjusted with different ratio. In mix design 3-4, W/C was slightly increased to 0.31 to improve the fluidity of the materials. By using the design, the material was continuously printed without clogging. Therefore, the optimum ratio is found to be 0.1% of the fiber that print material without clogging or shrinkage crack.
Adding PVA fibers to the mortar resulted in firmer output, as shown in Fig. 8. The hollow wall was successfully hardened without any cracks or subsidence. Moreover, layers were successfully stacked onto each other. The experiment took approximately 50 min to print the wall with a final height of 633 mm and a total of 96 printed layers.
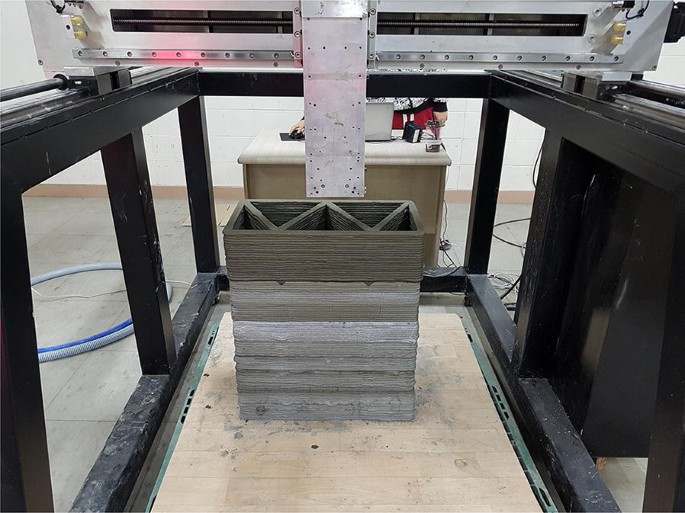
Constructed hollow walls with mortar containing PVA fibers.
Full size image
The experimental trials were focused on finding optimal ratio of the mix design for dispensing, and layering of the cementitious materials and printing the hollow wall. After the experiments, compressive strength test was conducted for the two mixtures which resulted in success of printing the wall using the BS standard. The compressive strengths for the mix design 3-3 and 3-4 were 60.4 MPa and 62 MPa respectively as shown in Table 4. The target compressive strength of the material was set as 50 MPa that met the target strength. Future experiment will involve measuring compressive strength of 3D printed specimens by either coring or nondestructive testing.
Full size table
Control Aspect
Various settings of 3D printers are another important aspect on printing with cementitious materials such as a motion speed of the nozzle, a rotational speed of a screw, a size of the nozzle tip and the height of the nozzle. Even when the same cementitious mixture is used, performances of FDM type 3D printings provide very different results by changing height with a nozzle speed and diameter of nozzle tip. According to Panda et al. (2018), tensile bond strength decreased as the printing speed or distance of nozzle standoff is increased emphasizing that the setting is important for the printing. Therefore, a 50-cm-long specimen was printed in several trials in order to verify effects of different settings including screw rotational speed and the height of the nozzle before printing the walls.
First, the trials were focused on finding the adequate motion speed and rotational speed of a screw. The motion speed is determined by the moving speed of the material within the nozzle while the rotational speed of the screw is determined by the amount of materials dispensed from the nozzle. The nozzle motion speed should not be too high related to rotational speed to avoid discontinuity of material flow, which is a major factor to cause defects in printing objects. It is important to note that discontinuity is a different phenomenon from cracking. A discontinuity occurs in the liquid (fluid) state, while cracking occurs during the process of hardening and curing. Moreover, the discontinuity is related to the tensile strength of concrete mortar as it is in a viscous semi-liquid state before solidification. The mortar with higher viscosity requires more power to drive (rotate) the screw used for extrusion. During the experiment, the materials were dispensed continuously with constant amount at an average motion speed of nozzle of 105 mm/s and a rotational speed of a screw of 9.55 rpm. Further study related to the motion speed and rotational speed is required to understand their correlation and synchronize material control.
After finding adequate setting of the motion speed and the rotational speed of a screw, the test was performed to find optimal height of the nozzle, distance between the nozzle tip and the base level, as shown in Fig. 9. When the height of the nozzle was too low compare to the amount of materials dispensed, the central part of the specimen was pressed and flattened increasing the total width while the nozzle tips scratch the surfaces as shown in Fig. 9a. When the height is too high, the specimen was printed to form a trapezoid shape with a wide base tapering to a narrow top as shown in Fig. 9c. When the height is at its optimum level as shown in Fig. 9b, the surface of the specimen was smooth with a rectangular shape. Based on the observations, it is determined that the optimal height is 7 mm with the motion speed of 105 mm/s and the rotational speed of a screw of 9.55 rpm for the material.
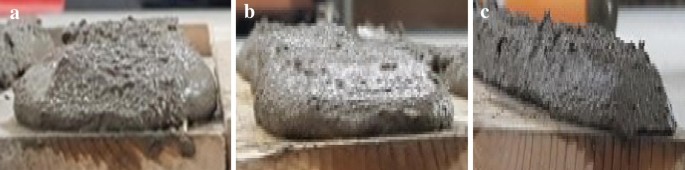
Surface of the specimens: when the nozzle is a low b adequate and c high.
Full size image
Other Aspects
Open time is one of the important aspects to determine the workability of the 3D printing with cementitious materials. Open time is the period of time that the cementitious material is dispensed continuously through the nozzle without stopping or clogging. In the research, the open time is determined by measuring the period of time that the material is extrudable continuously. Referring to the results from the material experiments, the slump flow spread of printing materials should maintain 190 mm to 200 mm to dispense the material constantly. Therefore, slump flow test was performed every 5 min to measure when the slump flow spread becomes lower than 190 mm. As shown in the graph in Fig. 10, the slump flow spread of the mix exhibited a gradual decrease and reached at 190 mm after 15 min. Thus, it is expected that the material is not extrudable after 15 min when the material reaches its open time limit. It is difficult to print the materials after the limit that a fresh mix of the material is required to print continuously. However, the open time can be controlled by adding the dosage of superplasticizer, retarder and accelerator that future experiment will involve materials with admixtures to test their influences (Le et al. 2012; Malaeb et al. 2015).
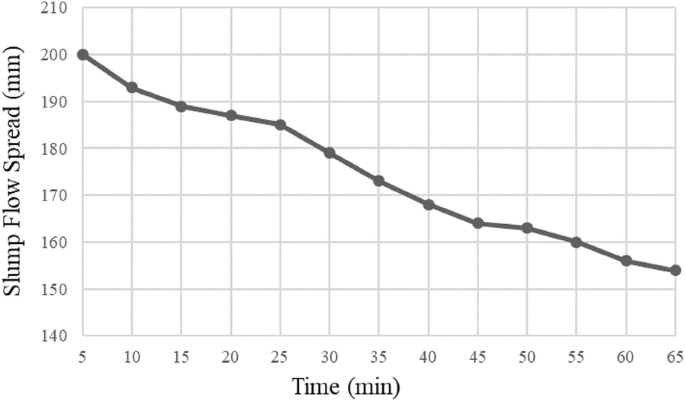
Slump flow spread of the cementitious material with time.
Full size image
Also, the critical characteristic that has a high impact on the bonding of layers is the time interval between printing of the layers. Each printed layers are expected to bond with other layers while it does not become an independent entity. The time interval is dependent on the performances of the material and the printing time of each layer. A balance between the parameters is a key factor in layering the material. If multiple layers are printed too fast with a low workability and a short time interval between the layers, sinking deformation can be occurred due to the weights of upper layers as shown in Fig. 11. On the contrary, if too much time interval is used for printing between the layers, a bond strength between the layers can be reduced (Panda et al. 2018; Le et al. 2012).
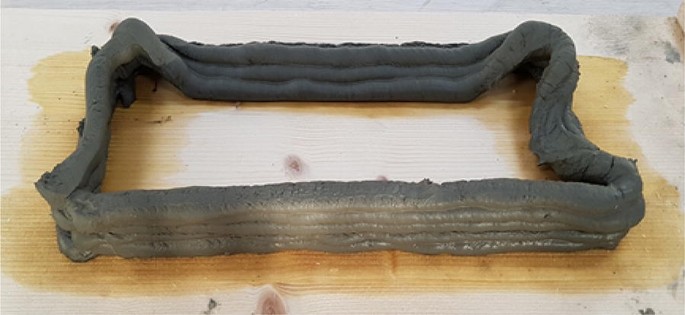
Sinking deformation of layers.
Full size image
Thus, the experiment was performed to investigate an influence of the time interval for the material used for printing the hollow wall. The material was printed with three different time intervals between printing layers: 15, 30 and 60 min. As the open time limit is 15 min, a fresh mix of the material was recharged to test time interval of 30 and 60 min. After printed specimens are hardened, the vertical cross sections of the specimens were compared referring in Fig. 12. For the specimen with 15 min of the time interval, the layers were well bonded together as shown in Fig. 12a. However, only the surfaces exposed to the air are bonded while boundary lines of each layer is observed for the specimen with 30 min of the time interval as shown in Fig. 12b. The cross section for 60 min of the time interval showed each layer as a separate entity as shown in Fig. 12c. It was observed that the boundary line became more noticeable as the time interval increased. Based on the observations, the maximum time gap required between printing layers was found to be 15 min. In order to print a hollow wall continuously, the printing was stopped for every 15 min to add fresh mix of the material considering its open time limit and proper layering.
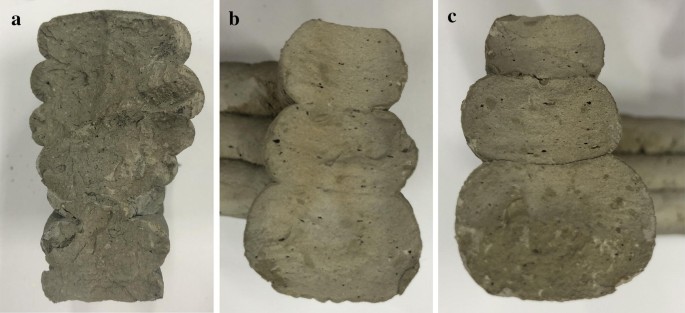
The cross section of the specimen with the time interval of a 15 min, b 30 min and 60 min.
Full size image
Using the aforementioned parameters, the width and height of the first layer were measured to be 15 mm and 7 mm, respectively. However, as more layers are added, the weight of the upper layers affected the height and width of the previous layers; while the height of the previous layers decreased, their width increased. After stacking several layers, the height and width of the first layer were re-measured and recorded as 17 mm and 4 mm, respectively. The initial ratio of width to height was 2.14, while the final ratio was found to be 4.25, which is a significantly increased value. These results suggest that, in structural design, the width to height ratio change should be taken into consideration to achieve the required final width and height of the part. Moreover, the nozzle diameter may also be varied to achieve the target width and height.
Conclusion
This research developed a prototype 3D printer for concrete structures at lab scale size, and its functionality was tested to find optimal material properties for the 3D printer. The conclusions are as follows.
First, a Cartesian FDM type of 3D printer with a linear servo motor was selected for the laboratory testing. Each motor attached to the printer controls distinctive axis independently. Each independently working motor enables more accurate printing and thus enhances the quality of printing.
Second, cementitious materials that have W/C ratio and a slump flow spread of 0.30 to 0.32 and 190 to 200 mm, respectively, were found to be optimal properties of the materials for extracting and layering the cementitious materials from the 3D printer by the laboratory testing.
Third, the testing proved that the adding 0.4 amount of sand, maximum size of 0.7 mm, relative to cement produced suitable mortal mix which did not cause any bleeding or clogging while printing. In case of dispensing larger size of sand or aggregates, further study will be required.
Fourth, the laboratory testing verified that adding 0.1% PVA fibers increased the quality of the printing by preventing shrinkage cracking. However, the higher percentage of fibers caused the screw inside the nozzle to malfunction.
Fifth, the open time is found to be 15 min for the materials. A fresh mix of the material was recharged every 15 min considering its open time and maximum time interval between printing layers.
Sixth, a compressive strength tests were conducted using the BS standard for the optimal cementitious material that the strength of two mixes were 60.4 MPa and 62 MPa. The cementitious materials found for the printing not only exceeded the target strength of 50 MPa, but also increased the quality of the overall product.
Seventh, motion control in the Cartesian coordinate system was implemented, and the nozzle parameters were manually controlled for printing. Nozzle movement was successfully controlled by the software, but implementation of feed control to the overall system control seems inevitable for full automation. Screw speed was not controlled. Further study on the relationship between screw speed and feed rate would be required to avoid defects such as discontinuity and clogging.
Availability of data and materials
Not applicable.
References
-
Ahmed, Z., Bos, F., Wolfs, R., & Salet, T. (2016). Design considerations due to scale effects in 3D concrete printing. In Proc. 8th the Arab Society for Computer Aided Architectural Design, London, United Kingdom.
-
Asprone, D., Auricchio, F., Menna, C., & Mercuri, V. (2018). 3D printing of reinforced concrete elements technology and design approach. Construction and Building Materials, 165, 218–231.
Article Google Scholar
-
Bos, F., Ahmed, Z., Justinov, E., & Salet, T. (2017). Experimental exploration of metal cable as reinforcement in 3D printed concrete. Materials, 10(11), 1314. https://doi.org/10.3390/ma10111314.
Article Google Scholar
-
Bos, F., Worlfs, R., Ahmed, Z., & Salet, T. (2016). Additive manufacturing of concrete in construction: Potentials and challenges of 3D concrete printing. Virtual and Physical Prototyping, 11(3), 209–225. https://doi.org/10.1080/17452759.2016.1209867.
Article Google Scholar
-
Gosselin, C., Duballet, R., Roux, Ph, Dirrenberger, J., & Morel, P. (2016). Large-scale 3D printing of ultra-high performance concrete—a new processing route for architects and builders. Materials and Design, 100, 102–109. https://doi.org/10.1016/j.matdes.2016.03.097.
Article Google Scholar
-
Henke, K., & Treml, S. (2013). Wood based bulk material in 3D printing processes for applications in construction. Europen Journal of Wood and Wood Products, 71, 139–141. https://doi.org/10.1007/s00107-012-0658-z.
Article Google Scholar
-
Kazemian, A., Yuan, X., Cochran, E., & Khoshnevis, B. (2017). Cementitious materials for construction-scale 3D printing: Laboratory testing of fresh printing mixture. Construction and Building Materials, 145, 639–647. https://doi.org/10.1016/j.conbuildmat.2017.04.015.
Article Google Scholar
-
Kim, H. (2017). Structural characteristics of 3D printing concrete form-liner and protective skin. M.S. Thesis, Kookmin University, Seoul, Korea.
-
Le, T., Austin, S., Lim, S., & Buswell, R. (2012). Mix design and fresh properties for high-performance printing concrete. Materials and Structures, 45, 1221–1232.
Article Google Scholar
-
Lee S (2017). Properties of waste incineration ash added cementitious material for possible usage in 3D printing. M.S. Thesis, Yonsei University, Seoul, Korea.
-
Lee, J., An, J., & Kai Chua, C. (2017). Fundamentals and applications of 3D printing for novel materials. Applied Materials Today, 7, 120–133. https://doi.org/10.1016/j.apmt.2017.02.004.
Article Google Scholar
-
Malaeb, Z., Hachem, H., Tourbah, A., Maalouf, T., El Zarwi, N., & Hamzeh, F. (2015). 3D Concrete printing: Machine and mix design. International Journal of Civil Engineering and Technology, 6(6), 14–22.
Google Scholar
-
Panda, B., Paul, S., Mohamed, N., Tay, Y., & Tan, M. (2018). Measurement of tensile bond strength of 3D printed geopolymer mortar. Measurement, 113, 108–116.
Article Google Scholar
-
Paul, S., Zijl, G., Tan, M., & Gibson, I. (2018). A review of 3D concrete printing systems and materials properties. Rapid Prototyping Journal, 24, 784–798.
Google Scholar
-
Perrot, A., Rangeard, D., & Pierre, A. (2016). Structural built-up of cement-based materials used for 3D printing extrusion techniques. Materials and Structures, 49, 1213–1220. https://doi.org/10.1617/s11527-015-0571-0.
Article Google Scholar
-
Seo, M., Ju, K., Kim, S., Ok, H., Moon, J., & Yang, S. (2014). Development of next generation construction fusion technology based on 3D printing. Internal Research Project Report, Seoul, Korea: Korea Institute of Civil Engineering and Building Technology.
-
Shakor, P., Sanjayan, J., Nazari, A., & Nejadi, S. (2017). Modified 3D printed powder to cement-based material and mechanical properties of cement scaffold used in 3D printing. Construction and Building Materials, 138, 398–409. https://doi.org/10.1016/j.conbuildmat.2017.02.037.
Article Google Scholar
-
Stansbury, J., & Idacavage, M. (2016). 3D printing with polymers: Challenges among expanding options and opportunities. Dental Materials, 32, 54–64. https://doi.org/10.1016/j.dental.2015.09.018.
Article Google Scholar
-
Tumbleston, J., Shirvanyants, D., Ermoshkin, N., Janusziewicz, R., Johnson, A., Kelly, D., Chen, K., Pinschmidt, R., Rolland, J., Ermoshkin, A., Samulski, E., DeSimone, J. (2015). Continuous liquid interface production of 3D objects. Research Report, Science, Washington D.C., United States of America.
-
Wang, X., Jiang, M., Zhou, Z., Gou, J., & Hui, D. (2017). 3D printing of polymer matrix composites: A review and prospective. Composites Part B: Engineering, 110, 442–458. https://doi.org/10.1016/j.compositesb.2016.11.034.
Article Google Scholar
-
Wei, M., Li, W., & Yang, J. (2018). State-of-the-art of 3D printing technology of cementitious-An emerging technique for construction. Science China Technological Sciences., 61, 475–495.
Article Google Scholar
Download references
Acknowledgements
Not applicable.
Funding
This research was supported by the International Research & Development Program of the National Research Foundation of Korea (NRF); 2018055642.
Ethics declarations
Competing interests
The authors declare that they have no competing interests.
Additional information
Publisher's Note
Springer Nature remains neutral with regard to jurisdictional claims in published maps and institutional affiliations.
Journal information: ISSN 1976-0485 / eISSN 2234-1315
Rights and permissions
Open Access This article is licensed under a Creative Commons Attribution 4.0 International License, which permits use, sharing, adaptation, distribution and reproduction in any medium or format, as long as you give appropriate credit to the original author(s) and the source, provide a link to the Creative Commons licence, and indicate if changes were made. The images or other third party material in this article are included in the article's Creative Commons licence, unless indicated otherwise in a credit line to the material. If material is not included in the article's Creative Commons licence and your intended use is not permitted by statutory regulation or exceeds the permitted use, you will need to obtain permission directly from the copyright holder. To view a copy of this licence, visit http://creativecommons.org/licenses/by/4.0/.
Reprints and Permissions
About this article
Cite this article
Jo, J.H., Jo, B.W., Cho, W. et al. Development of a 3D Printer for Concrete Structures: Laboratory Testing of Cementitious Materials. Int J Concr Struct Mater 14, 13 (2020). https://doi.org/10.1186/s40069-019-0388-2
Download citation
-
Received:
-
Accepted:
-
Published:
-
DOI : https://doi.org/10.1186/s40069-019-0388-2
Keywords
- 3D printing
- cementitious materials
- concrete structure
- mortar
- slump-flow test
3d Printing Concrete Design Cad
Source: https://ijcsm.springeropen.com/articles/10.1186/s40069-019-0388-2
Posted by: lecroyblescither55.blogspot.com
0 Response to "3d Printing Concrete Design Cad"
Post a Comment